Did you know that unplanned downtime can cost your business up to $260,000 an hour?
Every second of unplanned downtime is money down the drain, resulting in loss of productivity and customer trust. For many businesses, especially manufacturing, downtime happens due to mechanical equipment failure. But it can also take place in the office setting if, for example, the HVAC equipment goes down.
For your business to prosper, you don’t want to experience downtime at any time, if possible. But how do you achieve this ideal scenario? The key is preventative maintenance.
Here are some of the best practices to maximize the life cycle of machinery and achieve zero unplanned downtime.
Have a Planned Maintenance Program in Place
Gears, bearings, and other components experience wear and tear over time. Eventually, they may break down.
A planned maintenance program can help anticipate these changes. Instead of being reactive with the intervention, you can be more proactive. For example, you can replace parts on a schedule based on the predicted lifespan of essential components.
Kahnmechanical.com recommends routine servicing performed per the manufacturer’s standards and specifications. It’s best to commit to factory-recommended maintenance intervals to extend the life of your precious equipment.
Train Your Machinery Operators
Lack of training hurts both your machinery and employees. Untrained operators unknowingly cause equipment wear and tear. They can also be injured if they don’t know how to operate the machinery properly.
The planned maintenance program should include operator training. You should also consider revising the operator’s manual to simplify the language or make it more suitable for a specific task. A worker who understands their machine inside and out is more likely to respect their equipment.
Lubricate and Clean Mechanical Equipment
The function of a machine involves hundreds of moving parts working together. Lubricants reduce the friction around the components as they move. As a result, your equipment becomes more efficient and experiences less wear and tear.
Here are some useful tips about lubrication. Always check the lubricant level regularly and keep an eye out for leaks or grease build-up. Use the right type and amount of lubricant as stated in the operator’s manual.
Cleaning is as crucial as lubrication. The presence of contaminants may lead to parts corrosion and decreased efficiency. Regular cleaning should be a part of your preventive maintenance.
Monitor Equipment for Wear and Tear
Equipment wear and tear is inevitable. Component aging happens even if you take all the necessary precautions, albeit more slowly. That’s why you should always set aside some time to check all the parts for signs of wear and tear.
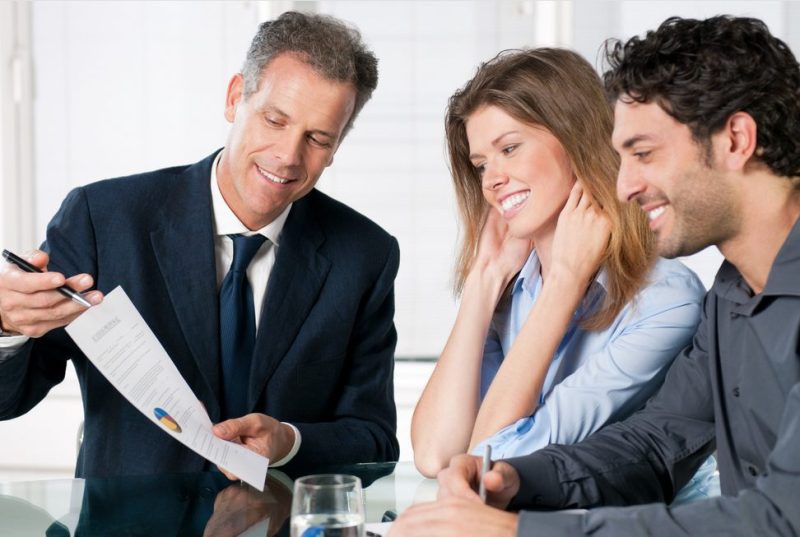
As mentioned, a planned maintenance program can often predict component wear. However, during checking, you might find out that some components need replacement ahead of schedule. There might be an underlying problem that needs to be identified as soon as possible.
Regular monitoring can help you uncover issues that may become more severe in the future.
Make Zero Unplanned Downtime Your Goal
To achieve zero unplanned downtime, you need to take care of your mechanical equipment. Follow the tips in this post to lengthen the lifespan and maximize the ROI of your machinery.
Please feel free to browse our site for more articles about business, lifestyle, health, tech, and other exciting topics.