Did you know that Jim Womack and Dan Jones finally captured the essence of why some lean organizations thrived while others failed?
It’s safe to say that lean manufacturing and lean waste are not on your list of topics to prepare for your upcoming round of Trivial Pursuit. But, these two areas of production and waste management are important.
The two boil down to increasing your output without increasing costs. Lean manufacturing has quite a few subcategories. Lean waste takes it one step further, asking what to do with what you’ve produced.
By learning more about them, you can make better-informed decisions.
Please read on for a guide to lean manufacturing and lean waste and how they can help you make your next product.
What is Lean Manufacturing?
Lean manufacturing is a process-based approach to manufacturing. These seek to cut waste and non-value-added activities. This is to increase efficiency and productivity.
The goal of lean manufacturing is to produce more with less. That is, to produce the same amount of output using fewer resources.
Lean production activities are more organized and streamlined to flow smoothly and continuously from one stage to the next.
Key Principles
A key principle of lean manufacturing is “flow.” This refers to the uninterrupted flow of materials and information. From the raw materials stage through to the finished product.
The concept of flow is also known as “pull” production. It is because lean production is “pulled” through the system by customer demand. Rather than being “pushed” through by production schedules.
Another key principle of lean manufacturing is “continuous improvement.” This refers to the constant strive to identify and cut waste. And non-value-added activities in the manufacturing process.
What is Lean Waste?
In business, Lean Waste is any activity or output that does not create value for the customer. This can include anything from unproductive steps in a manufacturing process. To paper waste in an office.
The goal of Lean is to cut or lessen all forms of waste to create a more efficient and effective organization.
The Benefits of Lean Waste
There are many benefits to reducing or cutting “wastes of lean”. The most obvious is the financial savings that are realized by streamlining operations. Including those reducing unnecessary costs.
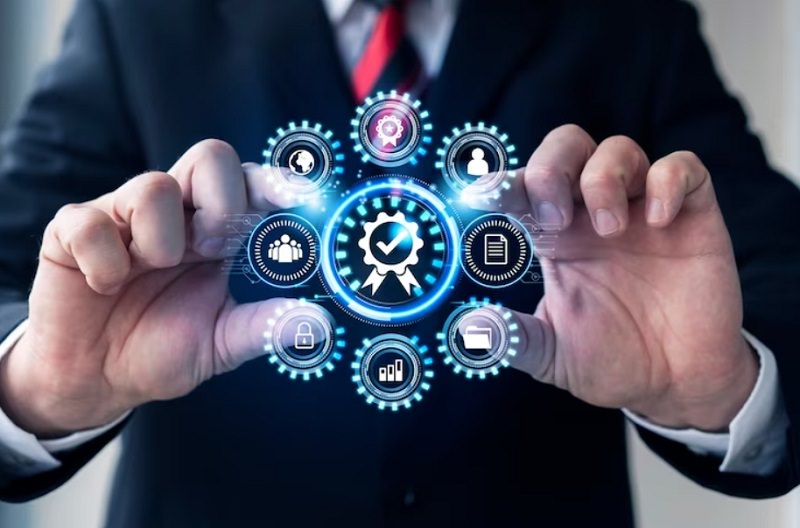
Also, lean organizations are often able to produce higher-quality products and services. As well as improve customer satisfaction by decreasing lead times and increasing responsiveness as a lean six sigma Green Belt.
Lean Waste is anything that gets in the way of an organization achieving its goals. By identifying and eliminating these sources of waste. Businesses can become more efficient, effective, and profitable.
Seven Types of Waste
Overproduction, inventory, motion, defects, over-processing, waiting, and transportation are the different types of waste.
A lean manufacturer is looking for ways to cut waste and increase value for the customer. This is through a continuous improvement process that involves all employees.
The goal of lean manufacturing is to produce more with less. – less waste, less time, less inventory, and fewer expenses. To achieve this, lean manufacturers must be willing to challenge the status quo and constantly look for ways to improve.
How to Implement Lean Manufacturing and Lean Waste
Here’s what you need to know about lean manufacturing. Lean Manufacturing and Lean Waste are two important concepts.
By reducing waste and improving efficiency, businesses can improve their bottom line. To learn more about Lean Manufacturing and Lean Waste, contact a local expert now.